Blog
Recent Posts
Evaluating whether to use a 3-axis, 4-axis, or 5-axis machine center
Posted on
Evaluating whether to use a 3-axis, 4-axis, or 5-axis machine center is an important decision in the field of manufacturing and machining. The choice largely depends on the complexity, precision requirements, and the desired efficiency of the machining process.
1. Understanding the Axes
First, it's crucial to understand what each axis represents:
- 3-Axis Machine Center: These machines operate on the X, Y, and Z axes, allowing for movement and cutting in three dimensions. They are suitable for a wide range of standard milling tasks.
- 4-Axis Machine Center: Adds an additional rotary axis, often referred to as the A-axis, which allows the workpiece to be rotated, enabling more complex shapes and features.
- 5-Axis Machine Center: Offers the most flexibility, with two additional axes (usually the A and B axes) that allow for the cutting tool to approach the workpiece from virtually any direction.
2. Evaluating Your Needs
- Complexity of Parts: If you are producing parts with complex geometries, undercuts, or require multi-face machining, a 4-axis or 5-axis machine may be necessary.
- Precision Requirements: For projects requiring high precision, especially in complex, contoured surfaces, 5-axis machines offer the best capabilities.
- Production Volume and Efficiency: Consider the volume of parts needed. 5-axis machines can reduce the setup time for complex parts, thus being more efficient for high-volume, complex jobs.
- Budget and Space Constraints: Higher-axis machines typically require more investment and space. Assess if the increased capabilities justify the cost and space required.
3. Upgrading a Milling Machine to 4-Axis or 5-Axis
- Adding a Rotary Table: One way to upgrade a 3-axis machine to 4-axis is by adding a rotary table. This table rotates the workpiece on an additional axis.
- Adding Tilt Rotary Tables: For 5-axis machining, a tilt rotary table that can rotate on two additional axes (tilting and rotating the workpiece) is required.
- Software Upgrade: Ensure that your CNC software can support 4-axis or 5-axis programming. Upgrading software is essential for effective operation.
- Calibration and Training: After upgrading, calibrate the machine correctly. Training for operators is also crucial, as 4-axis and 5-axis machining require more advanced programming and operational skills.
The choice between a 3-axis, 4-axis, or 5-axis machine center depends on the specific needs of your machining tasks. For simple parts, a 3-axis machine may suffice. As complexity and precision requirements increase, 4-axis and 5-axis machines become more advantageous. Upgrading a milling machine to handle more axes involves hardware additions, software upgrades, calibration, and training. It's a significant decision that should be based on a thorough analysis of your machining requirements, budget, and long-term production goals.
Headless Carr Lock® Clamps & Quick Change Carr Lock® Riser Demonstration
Headless CarrLock Clamps & Quickchange
Fixture Pins, their characteristics and functionality
When it comes to fixture pins used in CNC machine centers, assembly, and other manufacturing processes, there's a variety of types, each with different shapes, materials, and functionalities tailored to specific applications. Below is a synthesized overview of the types of fixture pins and their characteristics: Types of Fixture Pins and Their Characteristics: Cotter Pins: Shape: Typically a [...]
Carrlane Latch Action Toggle Clamps: Versatility and Functionality in Clamping
The industrial sector relies heavily on precision, durability, and efficiency. Whether it's about holding a component in place or ensuring secure fastening during manufacturing processes, the importance of a reliable clamping solution cannot be overstated. Among the myriad of clamping tools available, Carrlane's latch action toggle clamps have emerged as one of the leading choices [...]
Quick-Change Fixturing Systems: Spotlight on Roemheld and Carr Lane
In today's fast-paced manufacturing world, efficiency and speed are paramount. One area that has received significant attention is workholding, specifically the development of quick-change fixturing systems. These systems enable manufacturers to rapidly switch between different products or components, increasing production rates and reducing downtime. In this article, we will delve into the different types of [...]
Finished drill bushings vs producing them in-house
Choosing to buy finished drill bushings instead of manufacturing them in-house can be influenced by several factors, and here are a few reasons why purchasing might be preferred:1. Expertise and Quality: Manufacturers specializing in producing drill bushings have extensive expertise and experience.They can often produce higher quality and more precise bushings due to specialized knowledge, machinery, [...]
The Nuanced Approach to Designing Power Workholding Fixtures: Exploring the Merits of Pneumatic and Hydraulic Supports
In the vast realm of manufacturing and industrial applications, designing power workholding fixtures necessitates an astute grasp of various mechanisms and supports. Sometimes, incorporating pneumatic or hydraulic supports becomes not just a choice, but a requisite to ensure the efficiency and effectiveness of a fixture. Moreover, there lies a nuanced strategy in applying pressure from [...]
Designing Fixtures for Machine Centers: A Comprehensive Guide
In the manufacturing sector, the development of fixtures for machine centers is a pivotal process that demands meticulous planning and execution. Fixtures, which are employed to hold the workpieces in place during various machining operations, play a vital role in ensuring accuracy, repeatability, and efficiency of production. When designing fixtures for machine centers, several crucial [...]
Hydraulic vs. Pneumatic Clamping: A Focus on Swivel, Hinge, and Cylinder Body Clamps
Clamping systems are integral to a wide range of industrial and mechanical processes. Among the most prominent types are hydraulic vs. pneumatic clamping systems. When it comes to specialized clamps such as swivel clamps, hinge clamps, and cylinder body clamps, understanding the differences between hydraulic vs. pneumatic clamping can significantly affect the effectiveness of the [...]
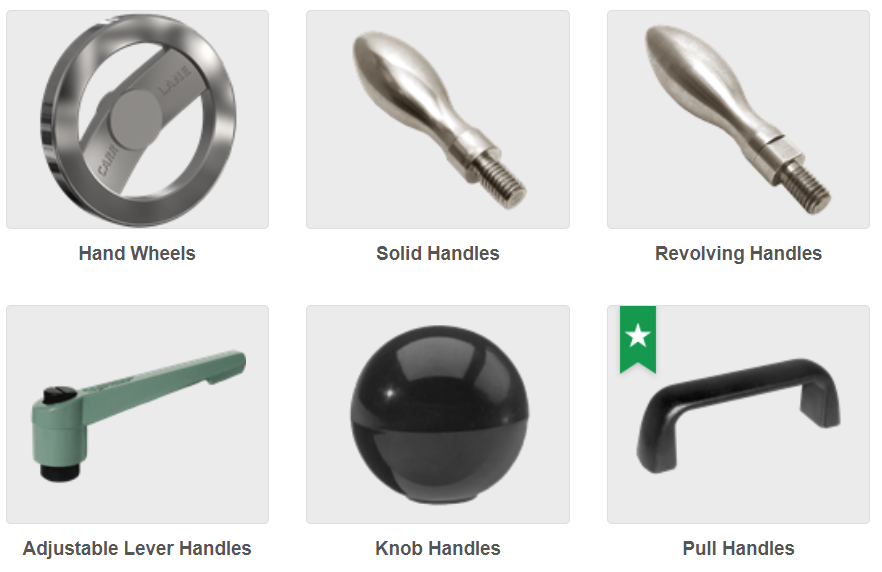
Carrlane Handles: Shapes and Fastening Types Explained
Carrlane offers a wide range of handles tailored to meet various needs in the engineering and mechanical industry. Their handles not only promise durability but also ease of use, catering to specific tasks and machinery. We will delve into the different shapes and fastening types of Carrlane handles.Shapes of Carrlane Handles1. Straight Handle Description: These handles [...]